Do gasless MIG welders work?
I'll answer
Earn 20 gold coins for an accepted answer.20
Earn 20 gold coins for an accepted answer.
40more
40more

Benjamin King
Works at the International Seabed Authority, Lives in Kingston, Jamaica.
As a welding expert with years of experience in the field, I can confidently say that gasless MIG welders, more accurately known as self-shielded MIG (SSMIG) welders, do indeed work and have been effectively utilized in various welding applications. They are a type of MIG welding process that utilizes a self-shielding flux-cored wire, eliminating the need for an external shielding gas, which is a common feature in traditional MIG welding.
What is SSMIG Welding?
SSMIG welding is a versatile and efficient welding process that is particularly useful for welding in positions that are difficult to access or where the use of shielding gas is impractical. It is a variation of the MIG (Metal Inert Gas) welding process, which is widely used for its ease of use and high-quality welds. The key difference lies in the type of wire used: SSMIG uses a flux-cored wire that provides its own shielding.
How Does SSMIG Work?
The self-shielding flux-cored wire is a hollow tube filled with a special type of flux. As the wire is fed into the welding torch and an electric arc is struck between the wire and the workpiece, the flux inside the wire melts. The melting flux reacts chemically to produce a shielding gas that surrounds the weld pool, protecting it from atmospheric contamination such as oxygen, nitrogen, and hydrogen. This shielding gas also helps to stabilize the arc and improve the overall quality of the weld.
Advantages of SSMIG Welding
1. No Need for External Shielding Gas: The primary advantage of SSMIG is that it does not require an external shielding gas, making it more portable and cost-effective.
2. Versatility: SSMIG can be used for welding in all positions, including vertical and overhead, where gas shielding can be challenging to maintain.
3. Ease of Use: For operators, SSMIG is often easier to use than traditional MIG welding, especially for those who are less experienced.
4. Improved Weld Quality: The self-shielding gas produced by the flux can lead to a cleaner weld with less spatter and better bead appearance.
5. Environmentally Friendly: Since no external gases are used, SSMIG is considered more environmentally friendly.
Limitations of SSMIG Welding
While SSMIG offers many benefits, it also has some limitations:
1. Limited to Certain Materials: SSMIG is typically best suited for welding carbon steel and low alloy steels. It may not be as effective for other materials like aluminum or stainless steel.
2. Higher Deposition Rates: SSMIG wires tend to have a higher deposition rate compared to gas-shielded MIG, which can lead to increased spatter if not managed properly.
3. Flux Residue: The flux used in SSMIG can leave a residue that may need to be cleaned off after welding, especially for applications where aesthetics are important.
Applications of SSMIG Welding
SSMIG is widely used in various industries, including construction, shipbuilding, automotive, and heavy machinery manufacturing. It is particularly useful for outdoor work, where the use of gas cylinders can be cumbersome, and for applications requiring high mobility.
Conclusion
In conclusion, gasless MIG welders, or more precisely, self-shielded MIG welders, are a viable and effective welding solution for many applications. They offer a combination of portability, ease of use, and quality that makes them an attractive option for many welders. As with any welding process, understanding the specific requirements of your project and the characteristics of the materials you are working with is crucial to achieving the best results.
What is SSMIG Welding?
SSMIG welding is a versatile and efficient welding process that is particularly useful for welding in positions that are difficult to access or where the use of shielding gas is impractical. It is a variation of the MIG (Metal Inert Gas) welding process, which is widely used for its ease of use and high-quality welds. The key difference lies in the type of wire used: SSMIG uses a flux-cored wire that provides its own shielding.
How Does SSMIG Work?
The self-shielding flux-cored wire is a hollow tube filled with a special type of flux. As the wire is fed into the welding torch and an electric arc is struck between the wire and the workpiece, the flux inside the wire melts. The melting flux reacts chemically to produce a shielding gas that surrounds the weld pool, protecting it from atmospheric contamination such as oxygen, nitrogen, and hydrogen. This shielding gas also helps to stabilize the arc and improve the overall quality of the weld.
Advantages of SSMIG Welding
1. No Need for External Shielding Gas: The primary advantage of SSMIG is that it does not require an external shielding gas, making it more portable and cost-effective.
2. Versatility: SSMIG can be used for welding in all positions, including vertical and overhead, where gas shielding can be challenging to maintain.
3. Ease of Use: For operators, SSMIG is often easier to use than traditional MIG welding, especially for those who are less experienced.
4. Improved Weld Quality: The self-shielding gas produced by the flux can lead to a cleaner weld with less spatter and better bead appearance.
5. Environmentally Friendly: Since no external gases are used, SSMIG is considered more environmentally friendly.
Limitations of SSMIG Welding
While SSMIG offers many benefits, it also has some limitations:
1. Limited to Certain Materials: SSMIG is typically best suited for welding carbon steel and low alloy steels. It may not be as effective for other materials like aluminum or stainless steel.
2. Higher Deposition Rates: SSMIG wires tend to have a higher deposition rate compared to gas-shielded MIG, which can lead to increased spatter if not managed properly.
3. Flux Residue: The flux used in SSMIG can leave a residue that may need to be cleaned off after welding, especially for applications where aesthetics are important.
Applications of SSMIG Welding
SSMIG is widely used in various industries, including construction, shipbuilding, automotive, and heavy machinery manufacturing. It is particularly useful for outdoor work, where the use of gas cylinders can be cumbersome, and for applications requiring high mobility.
Conclusion
In conclusion, gasless MIG welders, or more precisely, self-shielded MIG welders, are a viable and effective welding solution for many applications. They offer a combination of portability, ease of use, and quality that makes them an attractive option for many welders. As with any welding process, understanding the specific requirements of your project and the characteristics of the materials you are working with is crucial to achieving the best results.
2024-05-25 22:20:05
reply(1)
Helpful(1122)
Helpful
Helpful(2)
Works at Airbnb, Lives in San Francisco. Graduated from University of California, Berkeley with a degree in Marketing.
So called --Gasless-- Mig Wires are actually --Self Shielding--. Self Shielding Mig Wire is a tube of metal with a flux core. As the welding arc melts the wire it also burns the flux, this produces a gas shield around the welding process.Jan 12, 2018
2023-06-17 20:49:03
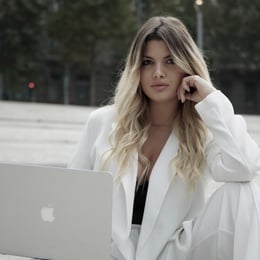
Zoe Wilson
QuesHub.com delivers expert answers and knowledge to you.
So called --Gasless-- Mig Wires are actually --Self Shielding--. Self Shielding Mig Wire is a tube of metal with a flux core. As the welding arc melts the wire it also burns the flux, this produces a gas shield around the welding process.Jan 12, 2018