What Tungsten is used for aluminum 2024?
I'll answer
Earn 20 gold coins for an accepted answer.20
Earn 20 gold coins for an accepted answer.
40more
40more

Julian Turner
Works at the United Nations Children's Fund (UNICEF), Lives in New York, NY, USA.
As a metallurgical engineer with a focus on welding and materials science, I specialize in understanding the properties and applications of various metals and their alloys. In the realm of welding, tungsten is a critical element due to its high melting point, excellent electrical conductivity, and its ability to withstand extreme temperatures without oxidizing. This makes it an ideal electrode material for processes like Tungsten Inert Gas (TIG) welding, which is particularly useful for welding aluminum and other non-ferrous metals.
When it comes to welding aluminum, the choice of tungsten is crucial for achieving a high-quality weld. The two types of tungsten electrodes mentioned, ceriated and 1.5% lanthanated, are both suitable for aluminum welding. The ceriated tungsten, identified by a gray band, is known for its ability to start arcs easily and for its longer life due to its self-sharpening properties. It is ideal for AC TIG welding of aluminum because it helps to stabilize the arc in the alternating current environment.
On the other hand, 1.5% lanthanated tungsten, marked by a gold band, offers a balance of good arc starting characteristics and electrode wear resistance. It is also suitable for welding aluminum, although it may require a slightly higher amperage to initiate the arc compared to ceriated tungsten.
For welding steel and stainless steel, a different approach is often taken. Here, DC-Straight Polarity (DCEN) is used, which is Direct Current Electrode Negative. This polarity is beneficial for welding ferrous materials because it provides deeper penetration and better control over the weld pool. In this case, a 2% thoriated tungsten, identified by a red band, is often preferred. Thoriated tungsten has a lower melting point than pure tungsten and provides a hotter, more easily started arc. However, it is worth noting that thoriated tungsten is being phased out in many regions due to health and environmental concerns associated with thorium, a radioactive material.
In summary, the selection of tungsten for welding aluminum revolves around the type of current used and the specific properties desired in the welding process. Ceriated and 1.5% lanthanated tungsten are both viable options for AC TIG welding of aluminum, providing ease of arc initiation and stability. For steel and stainless steel, DCEN with 2% thoriated tungsten is traditionally used, although it is facing regulatory challenges due to its radioactive component.
When it comes to welding aluminum, the choice of tungsten is crucial for achieving a high-quality weld. The two types of tungsten electrodes mentioned, ceriated and 1.5% lanthanated, are both suitable for aluminum welding. The ceriated tungsten, identified by a gray band, is known for its ability to start arcs easily and for its longer life due to its self-sharpening properties. It is ideal for AC TIG welding of aluminum because it helps to stabilize the arc in the alternating current environment.
On the other hand, 1.5% lanthanated tungsten, marked by a gold band, offers a balance of good arc starting characteristics and electrode wear resistance. It is also suitable for welding aluminum, although it may require a slightly higher amperage to initiate the arc compared to ceriated tungsten.
For welding steel and stainless steel, a different approach is often taken. Here, DC-Straight Polarity (DCEN) is used, which is Direct Current Electrode Negative. This polarity is beneficial for welding ferrous materials because it provides deeper penetration and better control over the weld pool. In this case, a 2% thoriated tungsten, identified by a red band, is often preferred. Thoriated tungsten has a lower melting point than pure tungsten and provides a hotter, more easily started arc. However, it is worth noting that thoriated tungsten is being phased out in many regions due to health and environmental concerns associated with thorium, a radioactive material.
In summary, the selection of tungsten for welding aluminum revolves around the type of current used and the specific properties desired in the welding process. Ceriated and 1.5% lanthanated tungsten are both viable options for AC TIG welding of aluminum, providing ease of arc initiation and stability. For steel and stainless steel, DCEN with 2% thoriated tungsten is traditionally used, although it is facing regulatory challenges due to its radioactive component.
2024-06-11 11:00:58
reply(1)
Helpful(1122)
Helpful
Helpful(2)
Works at Microsoft, Lives in Redmond, WA
When welding aluminum, use AC current and a ceriated (gray identifying band) or 1.5% lanthanated (gold identifying band) tungsten. When welding steel and stainless steel, use DC-Straight Polarity (DCEN) and a 2% thoriated (red identifying band) tungsten .
2023-06-12 20:48:57
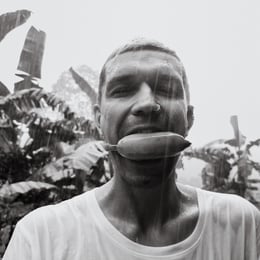
William Patel
QuesHub.com delivers expert answers and knowledge to you.
When welding aluminum, use AC current and a ceriated (gray identifying band) or 1.5% lanthanated (gold identifying band) tungsten. When welding steel and stainless steel, use DC-Straight Polarity (DCEN) and a 2% thoriated (red identifying band) tungsten .