Why are catalysts used during the cracking process 2024?
I'll answer
Earn 20 gold coins for an accepted answer.20
Earn 20 gold coins for an accepted answer.
40more
40more
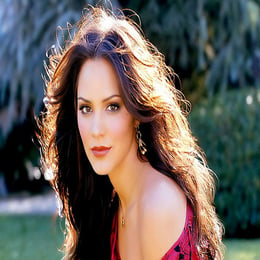
Harper Collins
Studied at the University of Oxford, Lives in Oxford, UK.
As a chemical engineer with experience in the petrochemical industry, I can provide an in-depth understanding of why catalysts are used in the cracking process.
Cracking is a critical process in petroleum refining that involves breaking down larger hydrocarbon molecules into smaller, more valuable ones. This process is essential for producing a range of products, including gasoline, diesel fuel, and other petrochemical feedstocks. The use of catalysts in the cracking process has revolutionized the industry, leading to significant improvements in efficiency, product quality, and environmental impact.
Fluid Catalytic Cracking (FCC) is the primary method of catalytic cracking used in refineries today. It is a continuous process that converts heavy hydrocarbons, such as vacuum gas oil, into lighter and more valuable products. The FCC process utilizes a catalyst to accelerate the chemical reactions that break down the hydrocarbon molecules.
The use of catalysts in the cracking process offers several key advantages:
1. Increased Efficiency: Catalysts lower the energy required to initiate and sustain the cracking reactions. This means that less heat is needed, which translates to lower operating costs and higher overall efficiency.
2. Improved Product Quality: The presence of a catalyst allows for more selective reactions, which can produce a higher yield of desired products, such as high-octane gasoline. This is particularly important as the demand for cleaner, more efficient fuels continues to grow.
3. Enhanced Reaction Rates: Catalysts increase the rate at which the cracking reactions occur. This allows for shorter residence times in the reactor, which can increase throughput and reduce the capital and operational costs associated with the process.
4. Environmental Benefits: By facilitating more efficient reactions, catalysts can help reduce the formation of unwanted byproducts and pollutants. This can lead to a cleaner refining process with fewer emissions.
5. Flexibility: The use of catalysts allows refineries to adjust the type and amount of catalyst used to tailor the product slate to market demands. This flexibility is crucial in an industry where product demand can fluctuate significantly.
6. Longevity and Regeneration: Many catalysts used in the cracking process can be regenerated, which means they can be reused multiple times. This not only reduces the environmental impact but also contributes to the economic viability of the process.
The original method of cracking petroleum hydrocarbons was through Thermal Cracking, which relied solely on heat to break the hydrocarbon molecules. However, this method has been largely replaced by catalytic cracking due to its limitations. Thermal cracking often resulted in a lower yield of gasoline and produced a product with a lower octane rating, which is less desirable for modern engines. Additionally, thermal cracking could lead to the formation of coke, which is a solid carbon residue that can foul equipment and reduce efficiency.
In contrast, catalytic cracking, particularly FCC, has become the preferred method due to its ability to produce a higher yield of gasoline with a higher octane rating. The use of a catalyst allows for the selective cracking of hydrocarbons into lighter, more valuable products, such as gasoline, while minimizing the formation of coke.
In summary, the use of catalysts in the cracking process is fundamental to modern petroleum refining. They enhance efficiency, improve product quality, increase reaction rates, offer environmental benefits, provide flexibility in product production, and can be regenerated for continued use. The transition from thermal to catalytic cracking has been a significant advancement in the industry, leading to more sustainable and economically viable refining practices.
Cracking is a critical process in petroleum refining that involves breaking down larger hydrocarbon molecules into smaller, more valuable ones. This process is essential for producing a range of products, including gasoline, diesel fuel, and other petrochemical feedstocks. The use of catalysts in the cracking process has revolutionized the industry, leading to significant improvements in efficiency, product quality, and environmental impact.
Fluid Catalytic Cracking (FCC) is the primary method of catalytic cracking used in refineries today. It is a continuous process that converts heavy hydrocarbons, such as vacuum gas oil, into lighter and more valuable products. The FCC process utilizes a catalyst to accelerate the chemical reactions that break down the hydrocarbon molecules.
The use of catalysts in the cracking process offers several key advantages:
1. Increased Efficiency: Catalysts lower the energy required to initiate and sustain the cracking reactions. This means that less heat is needed, which translates to lower operating costs and higher overall efficiency.
2. Improved Product Quality: The presence of a catalyst allows for more selective reactions, which can produce a higher yield of desired products, such as high-octane gasoline. This is particularly important as the demand for cleaner, more efficient fuels continues to grow.
3. Enhanced Reaction Rates: Catalysts increase the rate at which the cracking reactions occur. This allows for shorter residence times in the reactor, which can increase throughput and reduce the capital and operational costs associated with the process.
4. Environmental Benefits: By facilitating more efficient reactions, catalysts can help reduce the formation of unwanted byproducts and pollutants. This can lead to a cleaner refining process with fewer emissions.
5. Flexibility: The use of catalysts allows refineries to adjust the type and amount of catalyst used to tailor the product slate to market demands. This flexibility is crucial in an industry where product demand can fluctuate significantly.
6. Longevity and Regeneration: Many catalysts used in the cracking process can be regenerated, which means they can be reused multiple times. This not only reduces the environmental impact but also contributes to the economic viability of the process.
The original method of cracking petroleum hydrocarbons was through Thermal Cracking, which relied solely on heat to break the hydrocarbon molecules. However, this method has been largely replaced by catalytic cracking due to its limitations. Thermal cracking often resulted in a lower yield of gasoline and produced a product with a lower octane rating, which is less desirable for modern engines. Additionally, thermal cracking could lead to the formation of coke, which is a solid carbon residue that can foul equipment and reduce efficiency.
In contrast, catalytic cracking, particularly FCC, has become the preferred method due to its ability to produce a higher yield of gasoline with a higher octane rating. The use of a catalyst allows for the selective cracking of hydrocarbons into lighter, more valuable products, such as gasoline, while minimizing the formation of coke.
In summary, the use of catalysts in the cracking process is fundamental to modern petroleum refining. They enhance efficiency, improve product quality, increase reaction rates, offer environmental benefits, provide flexibility in product production, and can be regenerated for continued use. The transition from thermal to catalytic cracking has been a significant advancement in the industry, leading to more sustainable and economically viable refining practices.
2024-06-17 14:22:00
reply(1)
Helpful(1122)
Helpful
Helpful(2)
Studied at Columbia University, Lives in New York City. Entrepreneur passionate about social impact and currently running a nonprofit organization.
Fluid catalytic cracking (FCC) is one of the most important conversion processes used in petroleum refineries. ... Cracking of petroleum hydrocarbons was originally done by thermal cracking, which has been almost completely replaced by catalytic cracking because it produces more gasoline with a higher octane rating.
2023-06-08 17:27:18

Charlotte Harris
QuesHub.com delivers expert answers and knowledge to you.
Fluid catalytic cracking (FCC) is one of the most important conversion processes used in petroleum refineries. ... Cracking of petroleum hydrocarbons was originally done by thermal cracking, which has been almost completely replaced by catalytic cracking because it produces more gasoline with a higher octane rating.