What kind of grinding wheel for aluminum?
I'll answer
Earn 20 gold coins for an accepted answer.20
Earn 20 gold coins for an accepted answer.
40more
40more

Benjamin Martin
Works at the United Nations Office on Drugs and Crime, Lives in Vienna, Austria.
As a subject matter expert in the field of abrasives and grinding technology, I can provide you with a comprehensive answer regarding the selection of grinding wheels for aluminum.
When it comes to grinding aluminum, the choice of grinding wheel is crucial due to the material's unique properties. Aluminum is a non-ferrous metal that is relatively soft and has a tendency to heat up quickly, which can lead to melting or warping if not handled properly. Therefore, the selection of the grinding wheel must take into account the material's hardness, the desired finish, and the specific application.
The aluminum oxide (also known as corundum) grinding wheels are generally suitable for grinding various materials including aluminum. They offer a good balance of hardness and durability, which makes them ideal for general purpose grinding. Aluminum oxide wheels are available in different grit sizes, with finer grits being better for achieving a smoother finish.
Zirconia alumina grinding wheels, on the other hand, are known for their hardness and wear resistance. They are often used for precision grinding where a high level of accuracy is required. Zirconia alumina wheels are also suitable for aluminum, but they might be more expensive compared to aluminum oxide wheels.
For cast iron and non-ferrous metals, as well as non-metallic materials, silicon carbide abrasive wheels are often recommended. However, since aluminum is a non-ferrous metal, silicon carbide wheels can also be considered. These wheels are harder and more brittle than aluminum oxide wheels, which allows for faster cutting action and is beneficial for softer materials like aluminum.
When selecting a grinding wheel for aluminum, it's important to consider the grit size. A finer grit size (smaller numbers) will produce a smoother finish, while a coarser grit size (larger numbers) will remove material more quickly but may leave a rougher surface.
The grade of the wheel, which refers to the hardness of the wheel, is another important factor. A softer grade will wear faster but provide a cooler cut, which is beneficial for heat-sensitive materials like aluminum. A harder grade will last longer but may generate more heat, which can be detrimental to the workpiece.
Additionally, the bond type of the grinding wheel should be considered. Vitrified bonds are the most common and offer a good balance of strength and flexibility, while resinoid bonds are more flexible and provide a cooler cut, which can be advantageous for aluminum.
In summary, when choosing a grinding wheel for aluminum, consider the following factors:
1. Material Type: Aluminum oxide or zirconia alumina for general and precision grinding.
2. Grit Size: Finer grits for a smoother finish, coarser grits for faster material removal.
3. Grade: Softer grades for cooler cuts, harder grades for longer wheel life.
4. Bond Type: Vitrified for balance, resinoid for cooler operation.
It's also important to ensure that the grinding wheel is used with the proper safety equipment and procedures to prevent accidents and ensure the longevity of both the wheel and the workpiece.
When it comes to grinding aluminum, the choice of grinding wheel is crucial due to the material's unique properties. Aluminum is a non-ferrous metal that is relatively soft and has a tendency to heat up quickly, which can lead to melting or warping if not handled properly. Therefore, the selection of the grinding wheel must take into account the material's hardness, the desired finish, and the specific application.
The aluminum oxide (also known as corundum) grinding wheels are generally suitable for grinding various materials including aluminum. They offer a good balance of hardness and durability, which makes them ideal for general purpose grinding. Aluminum oxide wheels are available in different grit sizes, with finer grits being better for achieving a smoother finish.
Zirconia alumina grinding wheels, on the other hand, are known for their hardness and wear resistance. They are often used for precision grinding where a high level of accuracy is required. Zirconia alumina wheels are also suitable for aluminum, but they might be more expensive compared to aluminum oxide wheels.
For cast iron and non-ferrous metals, as well as non-metallic materials, silicon carbide abrasive wheels are often recommended. However, since aluminum is a non-ferrous metal, silicon carbide wheels can also be considered. These wheels are harder and more brittle than aluminum oxide wheels, which allows for faster cutting action and is beneficial for softer materials like aluminum.
When selecting a grinding wheel for aluminum, it's important to consider the grit size. A finer grit size (smaller numbers) will produce a smoother finish, while a coarser grit size (larger numbers) will remove material more quickly but may leave a rougher surface.
The grade of the wheel, which refers to the hardness of the wheel, is another important factor. A softer grade will wear faster but provide a cooler cut, which is beneficial for heat-sensitive materials like aluminum. A harder grade will last longer but may generate more heat, which can be detrimental to the workpiece.
Additionally, the bond type of the grinding wheel should be considered. Vitrified bonds are the most common and offer a good balance of strength and flexibility, while resinoid bonds are more flexible and provide a cooler cut, which can be advantageous for aluminum.
In summary, when choosing a grinding wheel for aluminum, consider the following factors:
1. Material Type: Aluminum oxide or zirconia alumina for general and precision grinding.
2. Grit Size: Finer grits for a smoother finish, coarser grits for faster material removal.
3. Grade: Softer grades for cooler cuts, harder grades for longer wheel life.
4. Bond Type: Vitrified for balance, resinoid for cooler operation.
It's also important to ensure that the grinding wheel is used with the proper safety equipment and procedures to prevent accidents and ensure the longevity of both the wheel and the workpiece.
2024-05-20 00:50:56
reply(1)
Helpful(1122)
Helpful
Helpful(2)
Works at the International Monetary Fund, Lives in Washington, D.C., USA.
For example, aluminum oxide or zirconia alumina should be used for grinding steels and steel alloys. For grinding cast iron, non-ferrous metals and non-metallic materials, select a silicon carbide abrasive. Hard, brittle materials generally require a wheel with a fine grit size and a softer grade.
2023-06-15 10:03:03
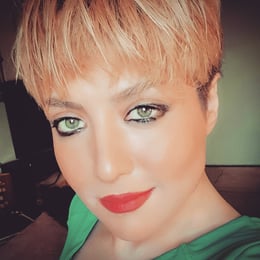
Zoe Campbell
QuesHub.com delivers expert answers and knowledge to you.
For example, aluminum oxide or zirconia alumina should be used for grinding steels and steel alloys. For grinding cast iron, non-ferrous metals and non-metallic materials, select a silicon carbide abrasive. Hard, brittle materials generally require a wheel with a fine grit size and a softer grade.