Can you use solder to weld aluminum?
I'll answer
Earn 20 gold coins for an accepted answer.20
Earn 20 gold coins for an accepted answer.
40more
40more

Ethan Rivera
Works at the International Atomic Energy Agency, Lives in Vienna, Austria.
As a metallurgical engineer with a focus on materials science, I've had extensive experience in the field of welding and joining various types of metals, including aluminum. Aluminum is a unique metal due to its high affinity for oxygen, which forms a protective oxide layer on its surface. This oxide layer, along with aluminum's low melting point compared to other metals, presents some challenges when it comes to soldering.
Soldering Aluminum: A Technical Overview
Soldering is a process where two or more metal items are joined together by melting and flowing a filler metal (solder) into the joint. The process is typically used for metals with relatively low melting points, such as lead and tin, which are commonly found in solders. However, aluminum's melting point is lower than that of most solders, which complicates the soldering process.
Choosing the Right Solder
When it comes to soldering aluminum, the choice of solder is critical. Traditional solders, which often contain tin, are not suitable for aluminum due to the risk of electrochemical corrosion. The galvanic potential between tin and aluminum can lead to accelerated corrosion, undermining the joint's integrity. Therefore, special solders are required for aluminum. These solders are typically formulated with elements like zinc, which can include trace amounts of lead, cadmium, tin, copper, or aluminum. The presence of zinc is beneficial as it forms a strong bond with aluminum and does not lead to the same corrosion issues as tin.
The Role of Flux
Flux plays a crucial role in the soldering process. It is a chemical cleaning agent that removes oxides and other impurities from the surfaces to be joined, allowing the solder to flow and adhere properly. However, some soft soldering fluxes can leave residues that remain active after the soldering process. These residues can be corrosive and must be removed to prevent damage to the aluminum. It's essential to use a flux that is compatible with aluminum and to clean the joint thoroughly after soldering.
Preparation and Technique
Before soldering aluminum, the surfaces must be meticulously cleaned to remove any oxide layer and prepare them for the soldering process. This often involves mechanical cleaning, such as sanding or wire brushing, followed by chemical cleaning to ensure all contaminants are removed.
The soldering technique itself must be carefully controlled. Since aluminum has a low melting point, the heat must be applied carefully to avoid melting the base metal. The soldering iron or torch must be used with precision to heat the joint just enough to melt the solder without overheating the aluminum.
Post-Soldering Considerations
After the soldering process, it's important to inspect the joint for any signs of poor adhesion or corrosion. If residues from the flux are present, they must be removed to prevent long-term damage. This can be done using a variety of cleaning solutions, depending on the type of flux used.
Conclusion
In conclusion, while soldering aluminum is more challenging than soldering other metals, it is possible with the right solder, flux, and technique. The key is to use a solder that contains zinc and to ensure thorough cleaning and careful application of heat during the soldering process. By taking these precautions, a strong and durable joint can be achieved.
Soldering Aluminum: A Technical Overview
Soldering is a process where two or more metal items are joined together by melting and flowing a filler metal (solder) into the joint. The process is typically used for metals with relatively low melting points, such as lead and tin, which are commonly found in solders. However, aluminum's melting point is lower than that of most solders, which complicates the soldering process.
Choosing the Right Solder
When it comes to soldering aluminum, the choice of solder is critical. Traditional solders, which often contain tin, are not suitable for aluminum due to the risk of electrochemical corrosion. The galvanic potential between tin and aluminum can lead to accelerated corrosion, undermining the joint's integrity. Therefore, special solders are required for aluminum. These solders are typically formulated with elements like zinc, which can include trace amounts of lead, cadmium, tin, copper, or aluminum. The presence of zinc is beneficial as it forms a strong bond with aluminum and does not lead to the same corrosion issues as tin.
The Role of Flux
Flux plays a crucial role in the soldering process. It is a chemical cleaning agent that removes oxides and other impurities from the surfaces to be joined, allowing the solder to flow and adhere properly. However, some soft soldering fluxes can leave residues that remain active after the soldering process. These residues can be corrosive and must be removed to prevent damage to the aluminum. It's essential to use a flux that is compatible with aluminum and to clean the joint thoroughly after soldering.
Preparation and Technique
Before soldering aluminum, the surfaces must be meticulously cleaned to remove any oxide layer and prepare them for the soldering process. This often involves mechanical cleaning, such as sanding or wire brushing, followed by chemical cleaning to ensure all contaminants are removed.
The soldering technique itself must be carefully controlled. Since aluminum has a low melting point, the heat must be applied carefully to avoid melting the base metal. The soldering iron or torch must be used with precision to heat the joint just enough to melt the solder without overheating the aluminum.
Post-Soldering Considerations
After the soldering process, it's important to inspect the joint for any signs of poor adhesion or corrosion. If residues from the flux are present, they must be removed to prevent long-term damage. This can be done using a variety of cleaning solutions, depending on the type of flux used.
Conclusion
In conclusion, while soldering aluminum is more challenging than soldering other metals, it is possible with the right solder, flux, and technique. The key is to use a solder that contains zinc and to ensure thorough cleaning and careful application of heat during the soldering process. By taking these precautions, a strong and durable joint can be achieved.
2024-05-20 04:40:34
reply(1)
Helpful(1122)
Helpful
Helpful(2)
Studied at the University of Queensland, Lives in Brisbane, Australia.
The residues of some soft soldering fluxes may be still active after soldering and must be removed. Solders used for aluminum generally contain zinc with some lead, cadmium, tin, copper, or aluminum. However, any solder that contains tin may cause an electrochemical corrosion problem due to its galvanic potential.
2023-06-17 05:18:14
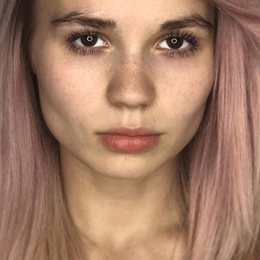
Charlotte Hill
QuesHub.com delivers expert answers and knowledge to you.
The residues of some soft soldering fluxes may be still active after soldering and must be removed. Solders used for aluminum generally contain zinc with some lead, cadmium, tin, copper, or aluminum. However, any solder that contains tin may cause an electrochemical corrosion problem due to its galvanic potential.