How do they make rubber bands?
I'll answer
Earn 20 gold coins for an accepted answer.20
Earn 20 gold coins for an accepted answer.
40more
40more
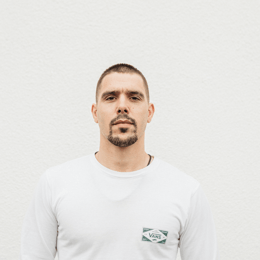
Adrian Nelson
Works at Dropbox, Lives in San Francisco, CA
Hello there! I'm a specialist in the field of materials science, with a particular focus on polymers and their applications. I'd be delighted to share with you the fascinating process of how rubber bands are made.
The production of rubber bands involves several key steps, starting from the extraction of natural rubber to the final packaging of the finished product. Let's delve into the details:
Extraction of Natural Rubber
The journey of a rubber band begins with the extraction of natural rubber from the Hevea brasiliensis tree, commonly known as the rubber tree. This tree is native to South America but is now cultivated in various tropical regions around the world. The process of extracting latex, the milky sap from which rubber is derived, involves tapping the tree's bark. This is done by making a shallow incision into the tree's bark, allowing the latex to flow out. The latex is then collected in cups or containers.
Coagulation and Drying
Once collected, the latex is subjected to a coagulation process, which involves adding an acid to the latex to cause it to solidify. This solidified rubber, known as crepe rubber, is then washed to remove impurities and any residual latex. After washing, the crepe rubber is pressed to remove excess water and then dried. The drying process can be done naturally by sun drying or mechanically in a drier.
Milling and Mixing
The dried rubber is then passed through a series of rollers in a mill to further refine its texture. During this stage, various chemicals and additives are mixed with the rubber. These additives may include vulcanizing agents, accelerators, and stabilizers, which are crucial for the rubber's performance and longevity.
Calendering
After mixing, the rubber is passed through a series of heated rollers in a process known as calendering. This process further refines the rubber's texture and consistency, making it smooth and uniform. The rubber is then cooled and cut into sheets of a specific thickness.
Extrusion and Cutting
The next step is extrusion, where the rubber sheet is pushed through a die to create long strands of rubber. These strands are then cut into smaller pieces, which will become the rubber bands. The cutting process can be done using a machine that cuts the rubber strands into loops or strips, depending on the desired shape of the rubber band.
Vulcanization
Vulcanization is a critical step in the production of rubber bands. It involves heating the rubber under controlled conditions to cross-link the polymer chains, which enhances the rubber's strength, elasticity, and durability. This process is typically carried out using steam or hot air.
Packaging
Finally, the rubber bands are sorted by size and quality, and then packaged for distribution. They can be sold in bulk or individually wrapped, depending on the intended use.
Throughout this process, it's important to note that quality control is a continuous and integral part of rubber band manufacturing. Each step is monitored to ensure that the final product meets the required specifications for elasticity, strength, and durability.
Now, let's move on to the next step.
The production of rubber bands involves several key steps, starting from the extraction of natural rubber to the final packaging of the finished product. Let's delve into the details:
Extraction of Natural Rubber
The journey of a rubber band begins with the extraction of natural rubber from the Hevea brasiliensis tree, commonly known as the rubber tree. This tree is native to South America but is now cultivated in various tropical regions around the world. The process of extracting latex, the milky sap from which rubber is derived, involves tapping the tree's bark. This is done by making a shallow incision into the tree's bark, allowing the latex to flow out. The latex is then collected in cups or containers.
Coagulation and Drying
Once collected, the latex is subjected to a coagulation process, which involves adding an acid to the latex to cause it to solidify. This solidified rubber, known as crepe rubber, is then washed to remove impurities and any residual latex. After washing, the crepe rubber is pressed to remove excess water and then dried. The drying process can be done naturally by sun drying or mechanically in a drier.
Milling and Mixing
The dried rubber is then passed through a series of rollers in a mill to further refine its texture. During this stage, various chemicals and additives are mixed with the rubber. These additives may include vulcanizing agents, accelerators, and stabilizers, which are crucial for the rubber's performance and longevity.
Calendering
After mixing, the rubber is passed through a series of heated rollers in a process known as calendering. This process further refines the rubber's texture and consistency, making it smooth and uniform. The rubber is then cooled and cut into sheets of a specific thickness.
Extrusion and Cutting
The next step is extrusion, where the rubber sheet is pushed through a die to create long strands of rubber. These strands are then cut into smaller pieces, which will become the rubber bands. The cutting process can be done using a machine that cuts the rubber strands into loops or strips, depending on the desired shape of the rubber band.
Vulcanization
Vulcanization is a critical step in the production of rubber bands. It involves heating the rubber under controlled conditions to cross-link the polymer chains, which enhances the rubber's strength, elasticity, and durability. This process is typically carried out using steam or hot air.
Packaging
Finally, the rubber bands are sorted by size and quality, and then packaged for distribution. They can be sold in bulk or individually wrapped, depending on the intended use.
Throughout this process, it's important to note that quality control is a continuous and integral part of rubber band manufacturing. Each step is monitored to ensure that the final product meets the required specifications for elasticity, strength, and durability.
Now, let's move on to the next step.
2024-05-20 06:40:09
reply(1)
Helpful(1122)
Helpful
Helpful(2)
Works at Facebook, Lives in Menlo Park, CA
While other rubber products may use synthetic rubber, most rubber bands are primarily manufactured using natural rubber because of its superior elasticity. Natural rubber originates from the latex of the rubber tree, which is acquired by tapping into the bark layers of the rubber tree.
2023-06-06 21:30:16

Isabella Lee
QuesHub.com delivers expert answers and knowledge to you.
While other rubber products may use synthetic rubber, most rubber bands are primarily manufactured using natural rubber because of its superior elasticity. Natural rubber originates from the latex of the rubber tree, which is acquired by tapping into the bark layers of the rubber tree.