Why quenching is done?
I'll answer
Earn 20 gold coins for an accepted answer.20
Earn 20 gold coins for an accepted answer.
40more
40more

Lucas Patel
Works at Amazon, Lives in Seattle, WA
As a materials science expert with a focus on metallurgy, I have extensive experience in the heat treatment of metals, particularly the process known as quenching. Quenching is a critical step in the production of steel and cast iron alloys, which are widely used in various industries due to their strength and durability. The process involves several key stages, each of which plays a vital role in achieving the desired material properties.
Step 1: Introduction to Quenching
Quenching, also known as "quench hardening," is a heat treatment technique used to alter the physical properties of ferrous metals, such as steel and cast iron. The process aims to increase the hardness and strength of these materials, making them more suitable for applications that require high wear resistance and load-bearing capacity.
Step 2: The Science Behind Quenching
The science behind quenching lies in the transformation of the metal's microstructure. When steel or cast iron is heated to a specific temperature, known as the "critical temperature," the material undergoes a phase change. At this temperature, the metal transitions from a soft, ferrite-pearlite structure to a harder, martensitic structure. This transformation is facilitated by the rapid cooling, or quenching, of the material.
Step 3: The Quenching Process
The quenching process typically involves three main steps:
1. Heating: The metal is heated to a temperature above its critical temperature, which is specific to the type of steel or cast iron being treated. This step is crucial as it ensures that the material is in a state conducive to the phase change.
2. Quenching: Once the material has reached the desired temperature, it is rapidly cooled, usually by immersing it in a quenching medium such as water, oil, or air. The rapid cooling rate is essential for the formation of the martensitic structure, which is characterized by its hardness and strength.
3. Tempering: After quenching, the material is often subjected to a process called tempering. This involves heating the material to a lower temperature and then cooling it slowly. Tempering helps to relieve internal stresses caused by the rapid cooling during quenching and can also improve the toughness of the material.
Step 4: Benefits and Applications
The benefits of quenching include increased hardness, strength, and wear resistance. These properties make quenched steel and cast iron alloys ideal for use in components that are subject to high levels of stress, such as gears, bearings, and automotive parts.
Step 5: Considerations and Challenges
While quenching is an effective method for enhancing the properties of steel and cast iron, it also presents certain challenges. For instance, the rapid cooling can lead to the formation of internal stresses, which may result in distortion or cracking of the material. Additionally, the process can be energy-intensive and may require careful control of the cooling rate to achieve the desired microstructure and properties.
In conclusion, quenching is a vital process in the metallurgical industry, enabling the production of high-strength and durable materials. By understanding the science behind quenching and carefully controlling the process parameters, manufacturers can produce components with the exacting specifications required for a wide range of applications.
Step 1: Introduction to Quenching
Quenching, also known as "quench hardening," is a heat treatment technique used to alter the physical properties of ferrous metals, such as steel and cast iron. The process aims to increase the hardness and strength of these materials, making them more suitable for applications that require high wear resistance and load-bearing capacity.
Step 2: The Science Behind Quenching
The science behind quenching lies in the transformation of the metal's microstructure. When steel or cast iron is heated to a specific temperature, known as the "critical temperature," the material undergoes a phase change. At this temperature, the metal transitions from a soft, ferrite-pearlite structure to a harder, martensitic structure. This transformation is facilitated by the rapid cooling, or quenching, of the material.
Step 3: The Quenching Process
The quenching process typically involves three main steps:
1. Heating: The metal is heated to a temperature above its critical temperature, which is specific to the type of steel or cast iron being treated. This step is crucial as it ensures that the material is in a state conducive to the phase change.
2. Quenching: Once the material has reached the desired temperature, it is rapidly cooled, usually by immersing it in a quenching medium such as water, oil, or air. The rapid cooling rate is essential for the formation of the martensitic structure, which is characterized by its hardness and strength.
3. Tempering: After quenching, the material is often subjected to a process called tempering. This involves heating the material to a lower temperature and then cooling it slowly. Tempering helps to relieve internal stresses caused by the rapid cooling during quenching and can also improve the toughness of the material.
Step 4: Benefits and Applications
The benefits of quenching include increased hardness, strength, and wear resistance. These properties make quenched steel and cast iron alloys ideal for use in components that are subject to high levels of stress, such as gears, bearings, and automotive parts.
Step 5: Considerations and Challenges
While quenching is an effective method for enhancing the properties of steel and cast iron, it also presents certain challenges. For instance, the rapid cooling can lead to the formation of internal stresses, which may result in distortion or cracking of the material. Additionally, the process can be energy-intensive and may require careful control of the cooling rate to achieve the desired microstructure and properties.
In conclusion, quenching is a vital process in the metallurgical industry, enabling the production of high-strength and durable materials. By understanding the science behind quenching and carefully controlling the process parameters, manufacturers can produce components with the exacting specifications required for a wide range of applications.
2024-05-25 12:43:36
reply(1)
Helpful(1122)
Helpful
Helpful(2)
Works at SpaceX, Lives in Cape Canaveral.
Quench hardening is a mechanical process in which steel and cast iron alloys are strengthened and hardened. These metals consist of ferrous metals and alloys. This is done by heating the material to a certain temperature, depending on the material.
2023-06-07 04:04:31
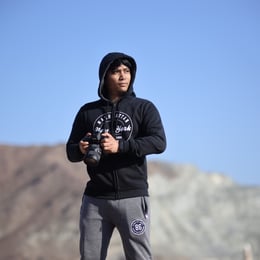
Benjamin Jackson
QuesHub.com delivers expert answers and knowledge to you.
Quench hardening is a mechanical process in which steel and cast iron alloys are strengthened and hardened. These metals consist of ferrous metals and alloys. This is done by heating the material to a certain temperature, depending on the material.